Wprowadzenie
Na przestrzeni lat w Polsce nastąpił znaczący rozwój sieci dróg i autostrad. Powstają coraz bardziej innowacyjne konstrukcje inżynierskie. Ze względu na duże koszty produkcji buduje się obiekty, które różnią się między sobą jedynie rodzajem powłoki zabezpieczającej i kolorem. Porównując rozwiązania funkcjonalne w innych krajach europejskich takich jak Niemcy bądź Francja, można dostrzec proste konstrukcje przy urozmaiceniu struktury powierzchni. Dzięki usunięciu powłok powierzchniowych można podziwiać piękno surowego betonu. W Polsce ten trend dopiero zaczyna się rozwijać [1]. W ubiegłym roku firma BETARD podjęła się realizacji znaczącego zamówienia na blisko ponad 900 belek mostowych typu T przy zastosowaniu betonu architektonicznego dla firmy Mostostal S.A na budowę obwodnicy Opatowa oraz łącznika północnego. Artykuł jest próbą przedstawienia sposobu realizacji zamówienia oraz przybliżenia tematyki dotyczącej produkcji betonu architektonicznego.
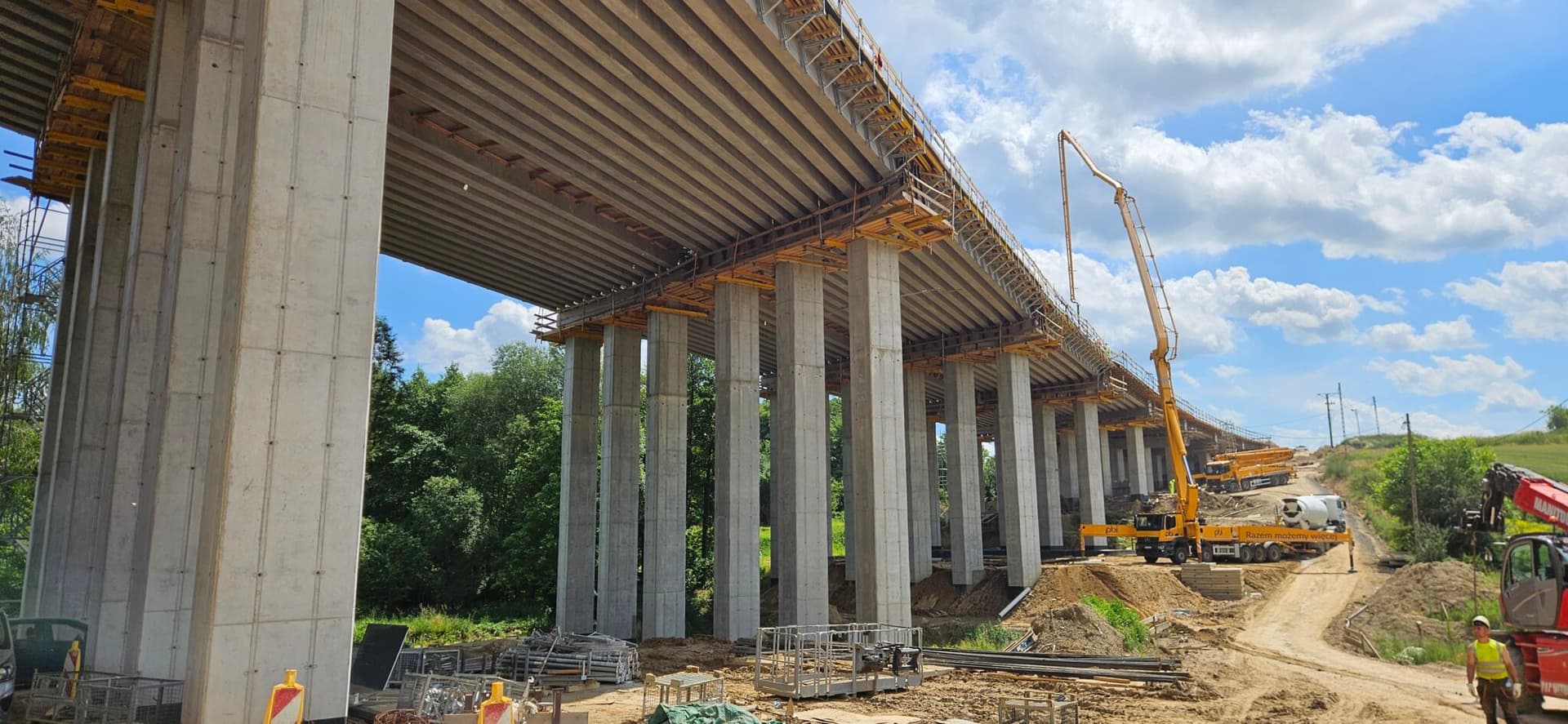
Produkcja
Zamówienie podzielone zostało na etapy. Budowa składała się z kilku obiektów, które powstawały w ustalonej kolejności. Produkcja belek działała z wyprzedzeniem co pozwalało na sprawną i efektywną realizację przedsięwzięcia. W zakładzie pracuje się w stałym schemacie czasowym zamkniętym w cyklu 24h, co spełnia wymagania klientów, a zarazem umożliwia realizację jak największej liczby zamówień. Na produkcję nawet 15 belek mostowych o długości ponad 20 m w ciągu doby pozwalają dwie połączone hale wyposażone w 6 torów naciągowych o długości 77 m i 84 m. Duże zamówienie oraz presja czasu wymagała ścisłej współpracy między brygadami, aby wyprodukować elementy w jak najlepszej jakości. Cały proces produkcyjny przedstawiony jest na poniższym schemacie [Rys. 1].
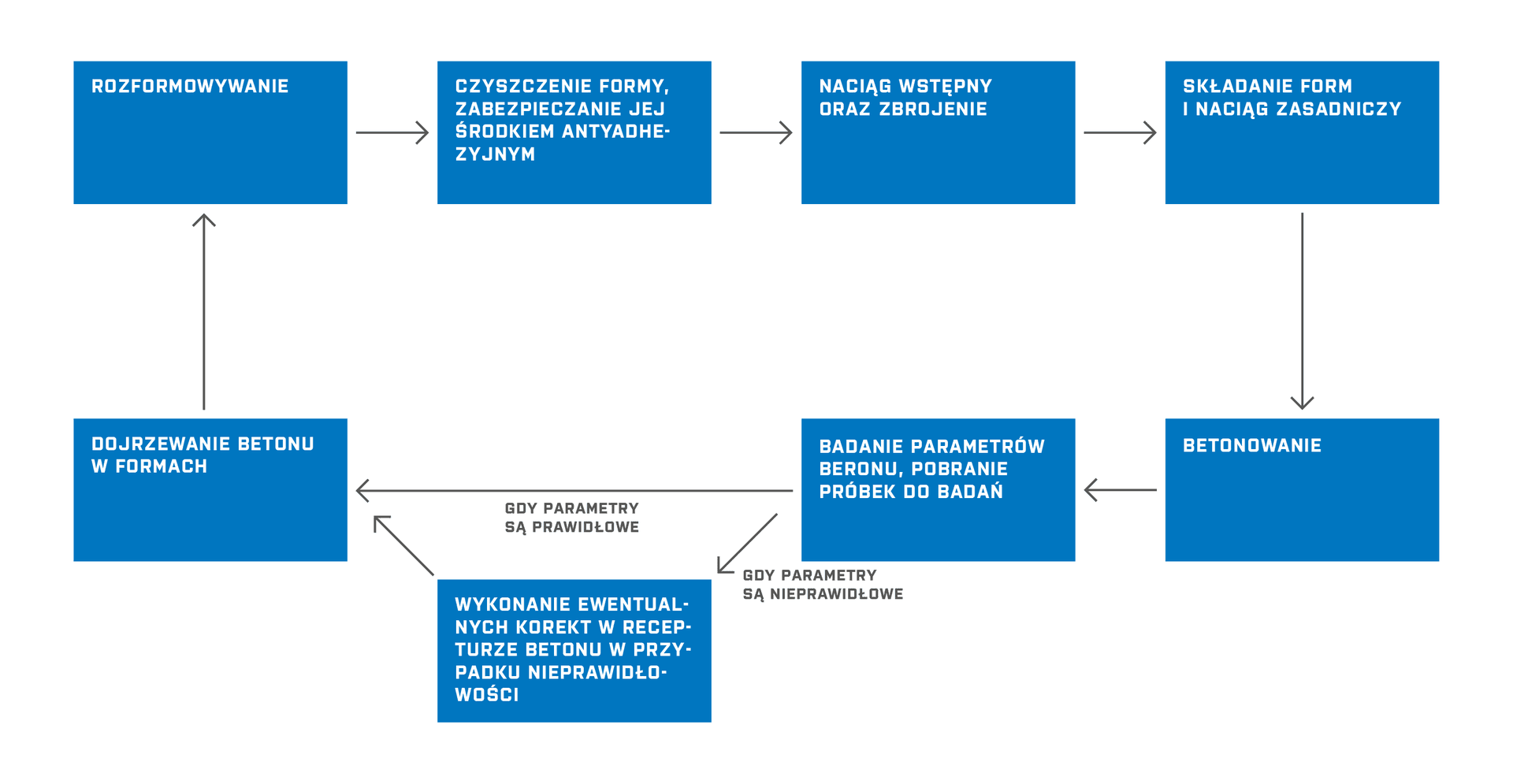
Do produkcji wykorzystano łącznie 1562,22 ton stali oraz 8609,45 m³ betonu. Od betonu do konstrukcji sprężonej oczekuje się dużej wytrzymałości na ściskanie. Do uzyskania mieszanki betonowej o wysokim module sprężystości konieczne jest zastosowanie kruszywa łamanego. Poza kruszywem istotne jest zastosowanie odpowiedniego cementu, zaprojektowanie jak najlepszej proporcji mieszanki betonowej oraz warunki dyfuzji wilgoci z betonu do otoczenia [2]. W celu uniknięcia typowych wad estetycznych mieszanki, kontrolowano czas transportu, monitorowano warunki środowiskowe oraz temperaturę obróbki cieplnej. Sposób transportu i czas jego trwania oraz metoda wbudowania i wibrowania zostały odpowiednio doszacowane dzięki odpowiedniej współpracy zespołów oraz wykonaniu wielu prób testowych. Uzyskanie jak najlepszej jakości powierzchni belek to również efekt prawidłowego przygotowania form przed betonowaniem [3]. Po każdym rozformowaniu formy są odpowiednio czyszczone z resztek betonu oraz taśm. Następnie aplikuje się środek antyadhezyjny dbając o to, aby środek został nałożony równomiernie i w odpowiedniej ilości. Niedopuszczalne są odparzenia powierzchni betonu.
Rozformowany element jest szczegółowo sprawdzany przez dział kontroli jakości. Kontroli podlega ilość i długość lin oraz prętów głównych, lokalizacja akcesoriów takich jak koboldy, otwory, rurki oraz wcięcia w półce na deski tracone, rozstaw i wymiar strzemion oraz długość belki w betonie. Dodatkowo sprawdzana jest powierzchnia belki, lokalizacja folii kubełkowej, obecność rys i pęknięć oraz czystość strzemion. Jeżeli kontrola przebiega pomyślnie i wszystkie wymiary mieszczą się w tolerancjach uwzględnionych w projekcie i deklaracji Właściwości Użytkowych to element jest zatwierdzany i transportowany na magazyn, gdzie następnie będzie przygotowywany do transportu [Fot. 2].
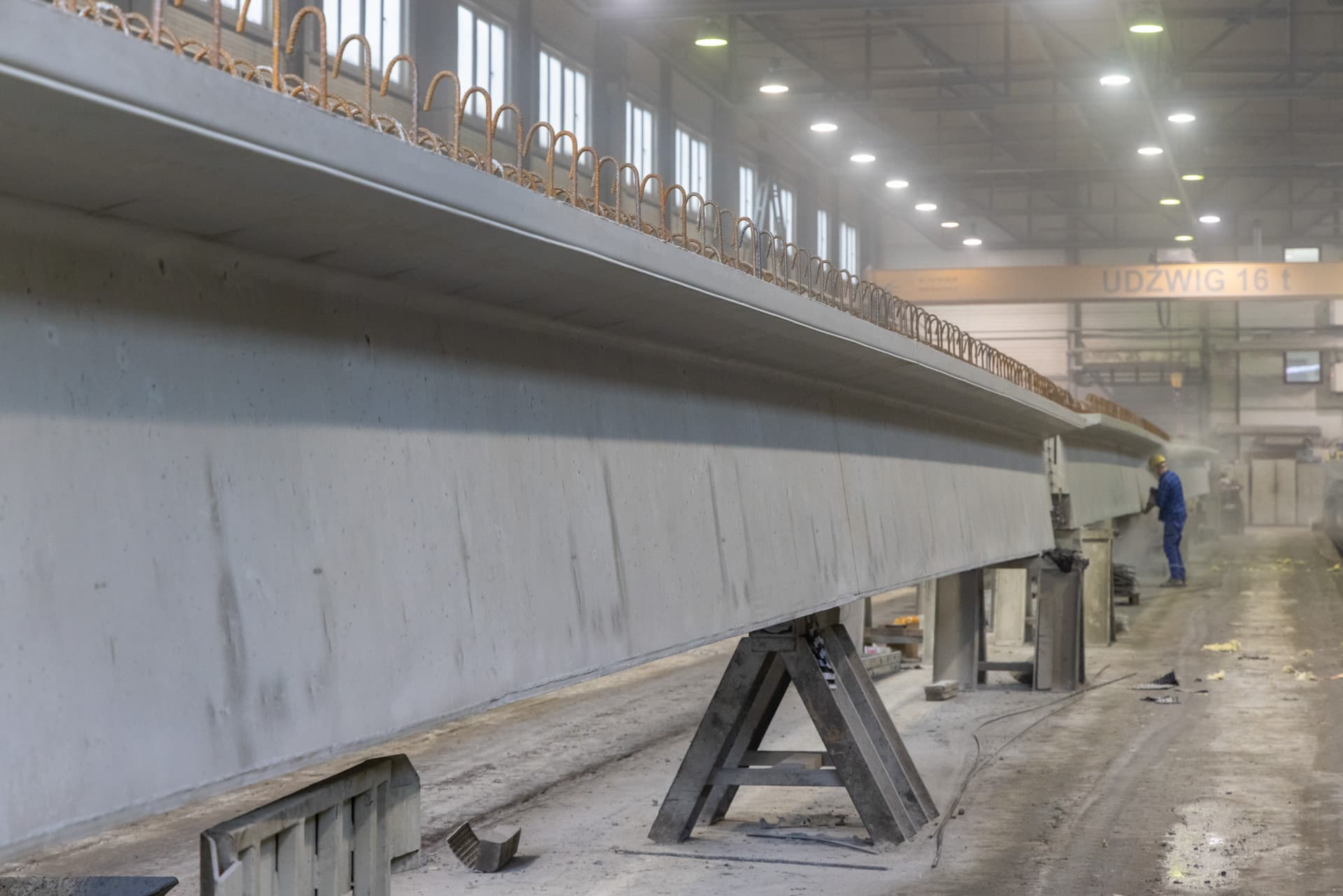
Sprawna komunikacja między zespołami gwarantuje szybką i efektywną produkcję przy jednoczesnym zachowaniu reżimu produkcyjnego. Na każdy element przyklejane są etykiety, na których są zawarte informacje takie jak: numer elementu, jego długość, dane zamawiającego i lokalizacja budowy oraz parametry betonu. Numeracja zaczyna się od nowa dla każdego nowego obiektu. Każdy element wraz z akcesoriami jest wpisywany do rejestru przez kontrolera, który po zakończeniu produkcji elementów dla całego obiektu sprawdza na podstawie projektu czy wszystkie belki zostały wyprodukowane oraz czy ilość akcesoriów się zgadza. Następnie przygotowuje schemat montażu. Zawiera on dane dotyczące kolejności montażu belek, numerację elementów wg. projektu jak również tą nadaną przez oddział, datę produkcji oraz strzałki ugięcia.
Te informacje pozwalają zarówno w sprawny i szybki sposób przygotować belki do transportu jak również pomagają w montażu belek bezpośrednio na budowie [Fot. 3].
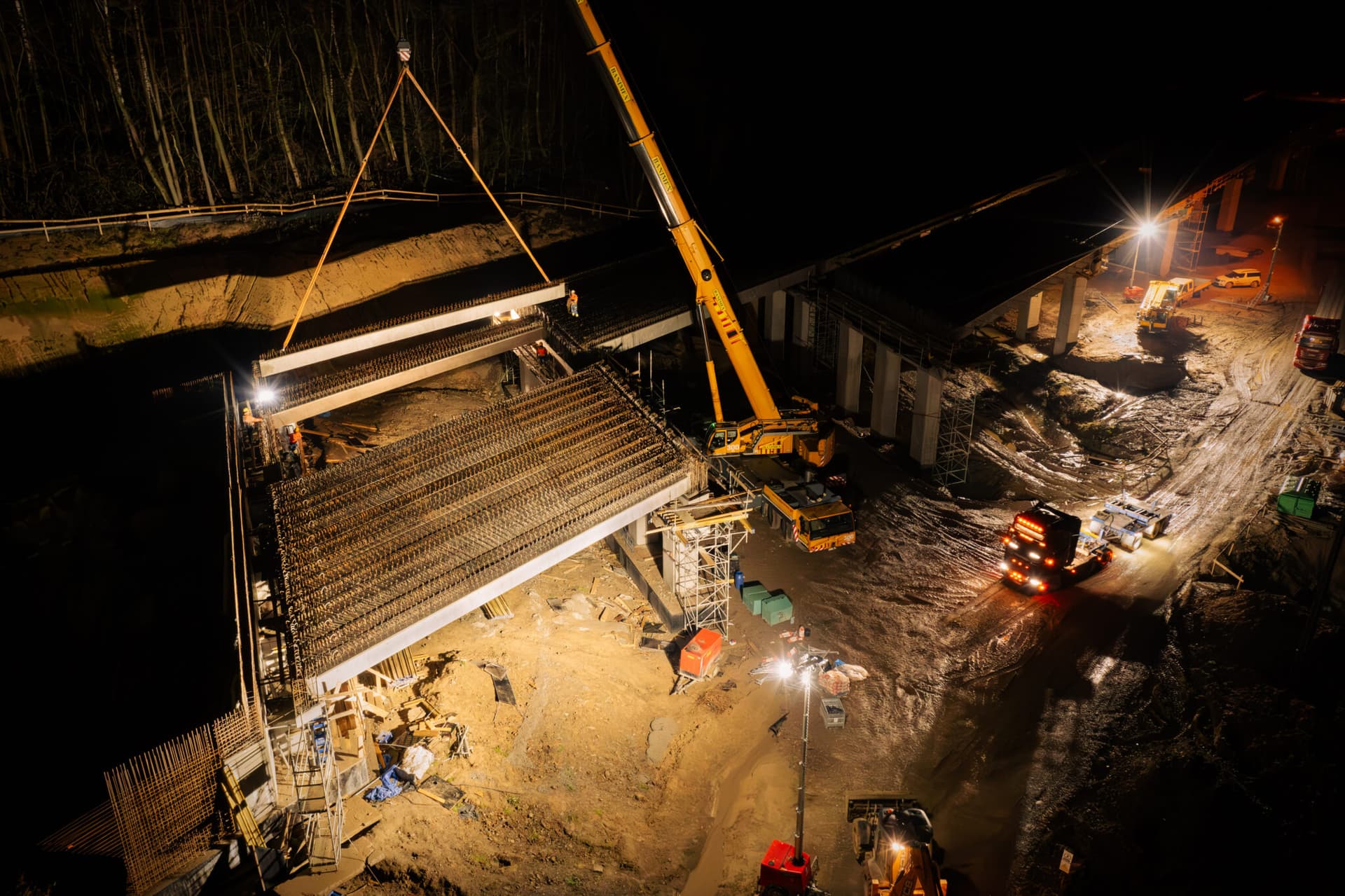
Badania
Wszystkie belki spełniały wymogi betonu architektonicznego BA2. Należy przez to rozumieć, że element po rozformowaniu pozostawia się go w naturalnej formie. W celu zapewnienia takich efektów betonu wymagana jest kontrola wszystkich powyższych procesów produkcyjnych. Dąży się do uniknięcia przebarwień, rys, zaschnięcia zaczynu na powierzchni formy oraz widocznych odcięć kolejnych partii betonu, w związku z tym receptura betonu jest wielokrotnie sprawdzana w laboratorium przed produkcją [4].
Podczas każdego betonowania pobierana została mieszanka do badań. Zespół laboratoryjny kontrolował zawartość powietrza w mieszance starając się utrzymać wynik na poziomie 4 – 6,5% zawartości powietrza w mieszance. Dodatkowo badano wytrzymałość na ściskanie po upływie 1 dnia oraz po 28 dniach. Co najmniej raz w miesiącu pobierano również próbki do zbadania głębokości penetracji wody w betonie oraz mrozoodporności. Do badań wykonano łącznie 2016 próbek o wymiarach 15x15x15 cm. Na badania przeznaczono około 6,8 m3 betonu o łącznej masie ponad 16 t. Oprócz tego regularnie kontrolowano parametry betonu kilkakrotnie podczas trwania betonowania zarówno w laboratorium oraz bezpośrednio na hali produkcyjnej. Monitorowano konsystencję i temperaturę mieszanki jak również sposób wlewania jej do form i wibrowanie.
Wszelkie nieprawidłowości były szybko naprawiane, aby utrzymać jak najlepsze parametry mieszanki przez cały przebieg produkcji [Tab. 1]. Wyniki badań przedstawiono poniżej [Tab. 2].
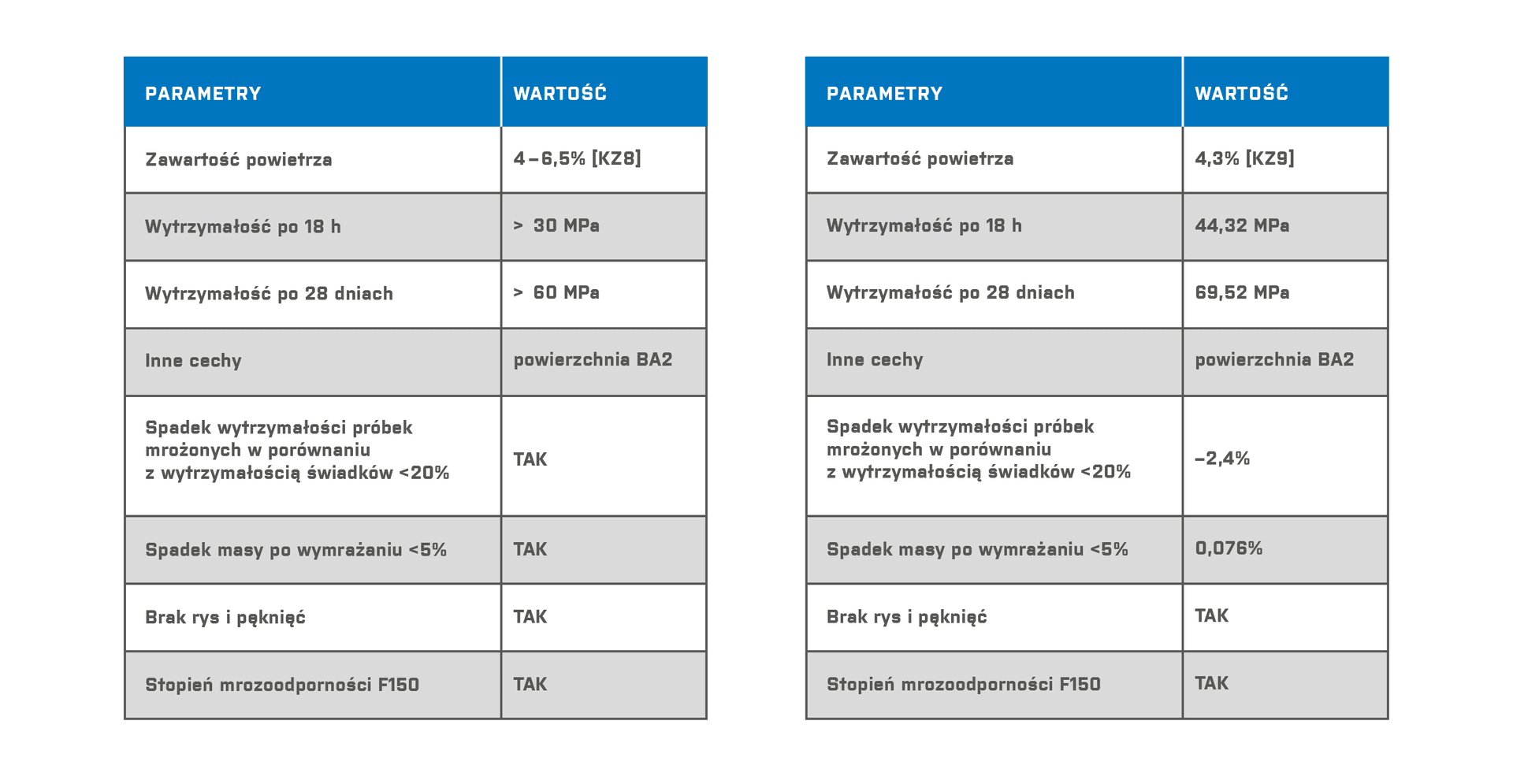
Magazynowanie i transport
Gotowy element transportowany jest z hali na magazyn. Belki są posegregowane według obiektów i układane są piętrowo. Dzięki temu na magazynie zachowany jest porządek co pozwala w szybki i sprawny sposób zlokalizować dany element i przygotować go do wysyłki oraz oszczędzane jest miejsce składowania w związku z tym możliwe jest magazynowanie większej liczby elementów. Cały teren składowiska pokryty jest betonową posadzką z lekkim spadkiem w celu szybkiego odwodnienia. Belki są ustawiane na specjalnych podkładkach dzięki czemu nie mają bezpośredniego kontaktu z podłożem. Zespół odpowiedzialny za składowanie elementów gotowych dba o to, aby wykluczyć wszelkie możliwości uszkodzeń lub zniszczeń prefabrykatów.
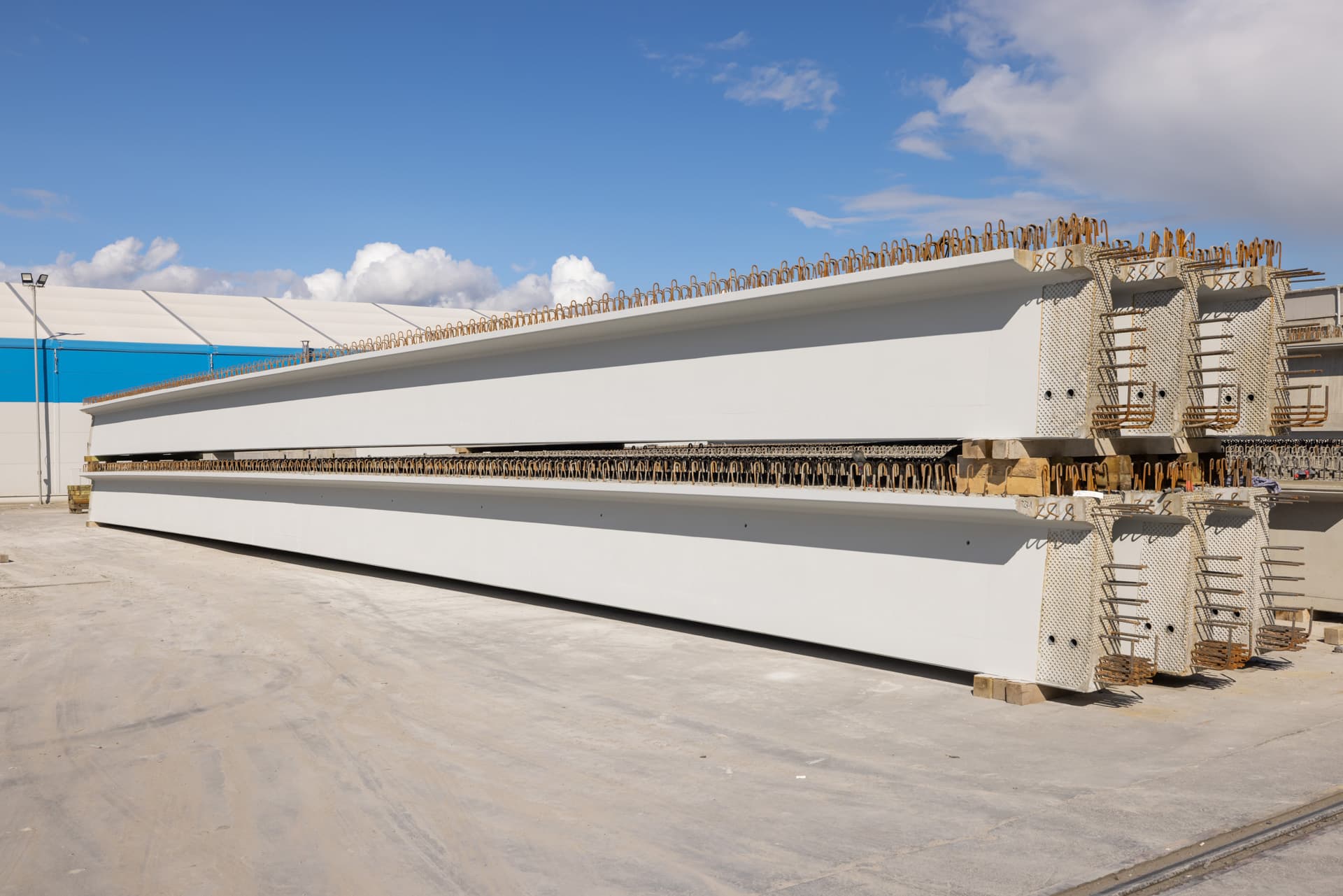
Tuż przed wyjazdem transportu na teren budowy kontrolerzy jakości po raz ostatni dokonują oceny wizualnej belek oraz sposobu ich zabezpieczenia na pojeździe. Zwraca się szczególną uwagę na to, aby każdy element opuścił element zakładu w jak najlepszym stanie i bez żadnych uszkodzeń bądź zabrudzeń.
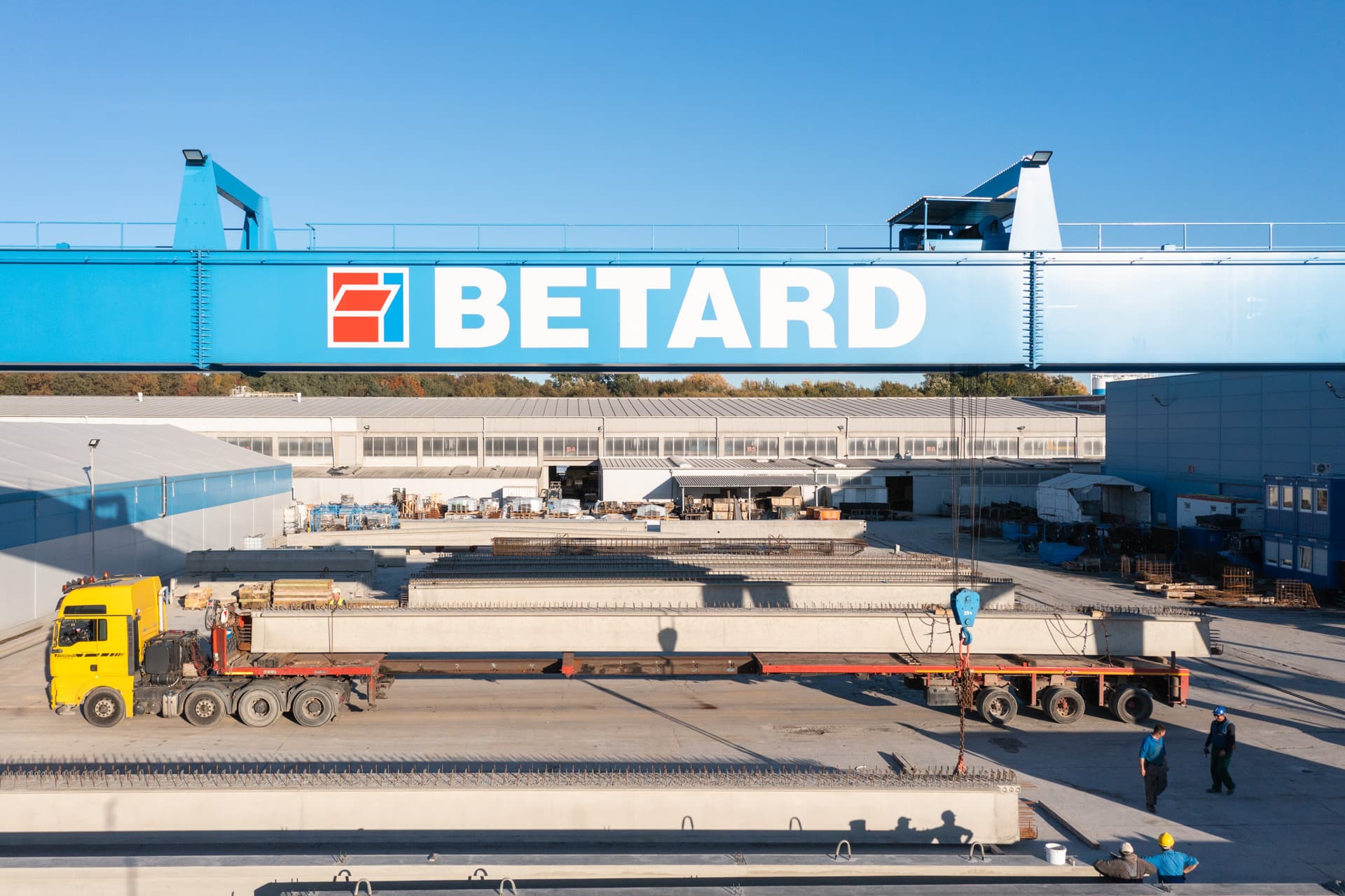
Podsumowanie
Dzisiejsza prefabrykacja nie ma nic wspólnego z negatywnymi opiniami, które krążyły w ubiegłych latach. Zakres wykorzystania prefabrykacji znacząco się powiększył ze względu na możliwości logistyczne oraz łatwość montażu. Analogicznie do krajów z zachodniej części Europy (Francja, Holandia, Niemcy) duży udział w rynku prefabrykatów w Polsce mają wyroby wielkowymiarowe jak np. prefabrykowane belki mostowe [5][6][7]. Na podstawie danych opublikowanych przez firmę SPECTIS można zaobserwować wzrost wartości rynku ciężkiej prefabrykacji. Prognozuje się, że w przeciągu kolejnych lat dynamika rynku będzie jeszcze większa [Wyk. 1].
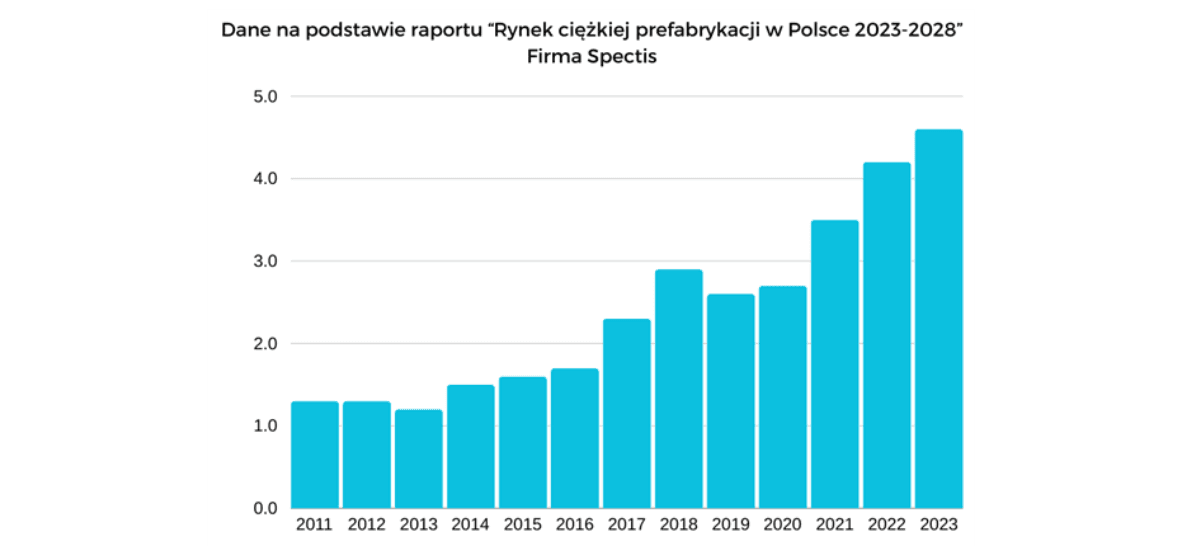
Z przedstawionego artykułu jednoznacznie wynika, że dzięki ciężkiej pracy i współpracy wielu zespołów oddział jest w stanie wyprodukować bardzo dużą ilość prefabrykatów o wysokiej jakości. Zdobyte doświadczenie i ciągły rozwój sprawiają, że firma jest gotowa na kolejne wyzwania w produkcji prefabrykatów mostowych.
Literatura:
- Beton architektoniczny w budownictwie mostowym Krzysztof Kuniczuk, Aldona Wcisło
- Beton-nowoczesność, funkcjonalność, estetyka, Maria Szruba, Nowoczesne Budownictwo Inżynieryjne 2018
- Prefabrykacja – jakość, trwałość, różnorodność. Grzegorz Adamczewski, Piotr Paweł Woyciechowski, Zeszyt 1. Stowarzyszenie Producentów Betonu, Warszawa 2014
- Beton Architektoniczny BA2 w prefabrykatach drogowo-mostowych, Krzysztof Zychowicz, 2023
- Betonowe Mosty Drogowe, Nakładem Polskich Fabryk Portland-Cementu, Warszawa 1930
- Prefabrykacja w Mostownictwie, prof. Dr hab. inż. Jan Biliszczuk, dr inż. Jerzy Onysyk 2016 r Nowoczesne Budownictwo Inżynieryjne
- Prefabrykaty w Budownictwie, Marian Kowacki, Nowoczesne Budownictwo Inżynieryjne, 2017