Autorzy:
Daria Ilkiewicz
Roksana Szmigielska
Stosowanie prefabrykatów betonowych w budownictwie mieszkaniowym przechodzi w ostatnich latach istotną ewolucję. Prefabrykacją można dzisiaj objąć całą konstrukcję budynku. Dzięki nowoczesnym rozwiązaniom produkcyjnym, automatyzacji, wysokiej jakości materiałom oraz doświadczeniu producentów obecnie można w tej technologii wykonać całą konstrukcję budynków, spełniając coraz surowsze wymogi projektowe oraz jednocześnie skrócić czas realizacji inwestycji.
W styczniu 2022 r. rozpoczęto budowę Miejskiego Stadionu w północno-zachodniej części Opola (fotografia 1 i 2), który ma służyć nie tylko piłkarskim rozgrywkom, ale także ma stanowić miejsce wydarzeń kulturalnych.
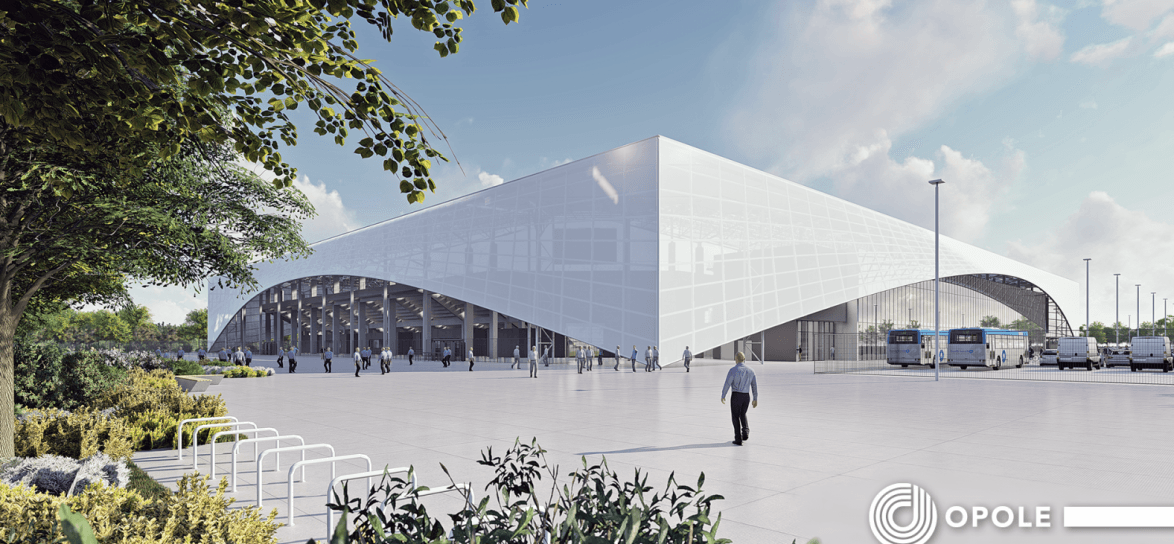
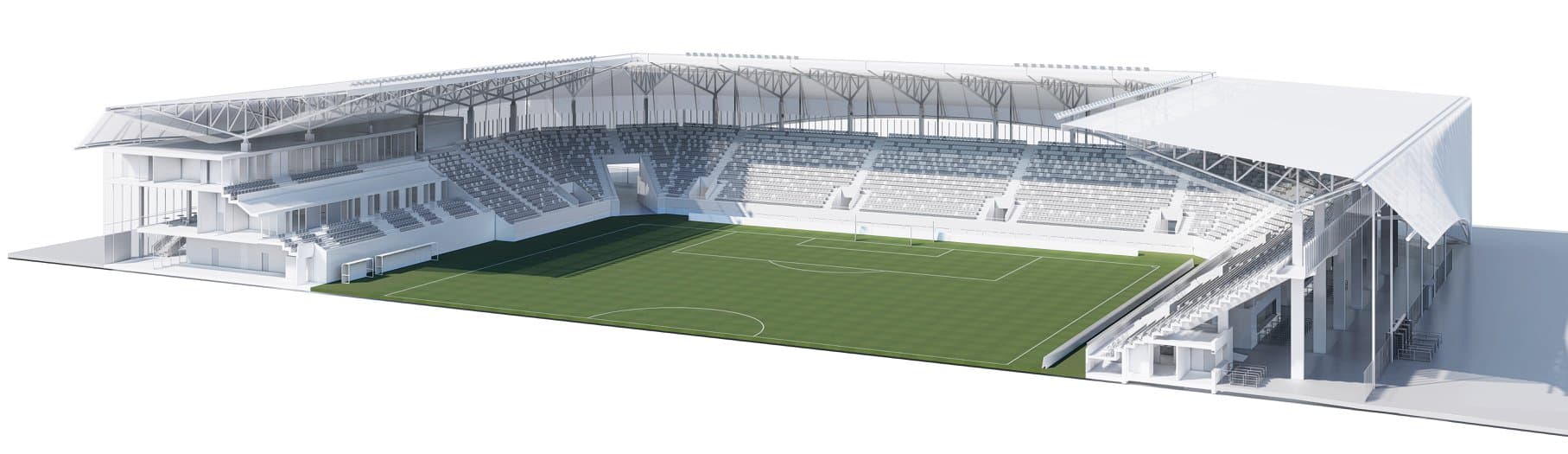
Docelowo obiekt pomieści 11,6 tys. widzów. Za projekt architektoniczny odpowiada biuro 90 Architekci, projekt wykonawczy opracowało biuro projektowe Matejko & Wesoły, a wykonawcą generalnym jest firma MIRBUD S.A. Szkielet konstrukcji stanowią elementy prefabrykowane (fotografia 3) produkowane przez firmę Betard, która specjalizuje się w wytwarzaniu nietypowych prefabrykowanych elementów betonowych. Elementy prefabrykowane tej firmy zastosowano m.in. na budowie Stadionu Olimpijskiego we Wrocławiu, Stadionu Żużlowego w Zielonej Górze, Hali Sportowej w Opolu (Toyota Park), Stadionu Miejskiego ŁKS Łódź mieszczącego 18 tys. widzów.
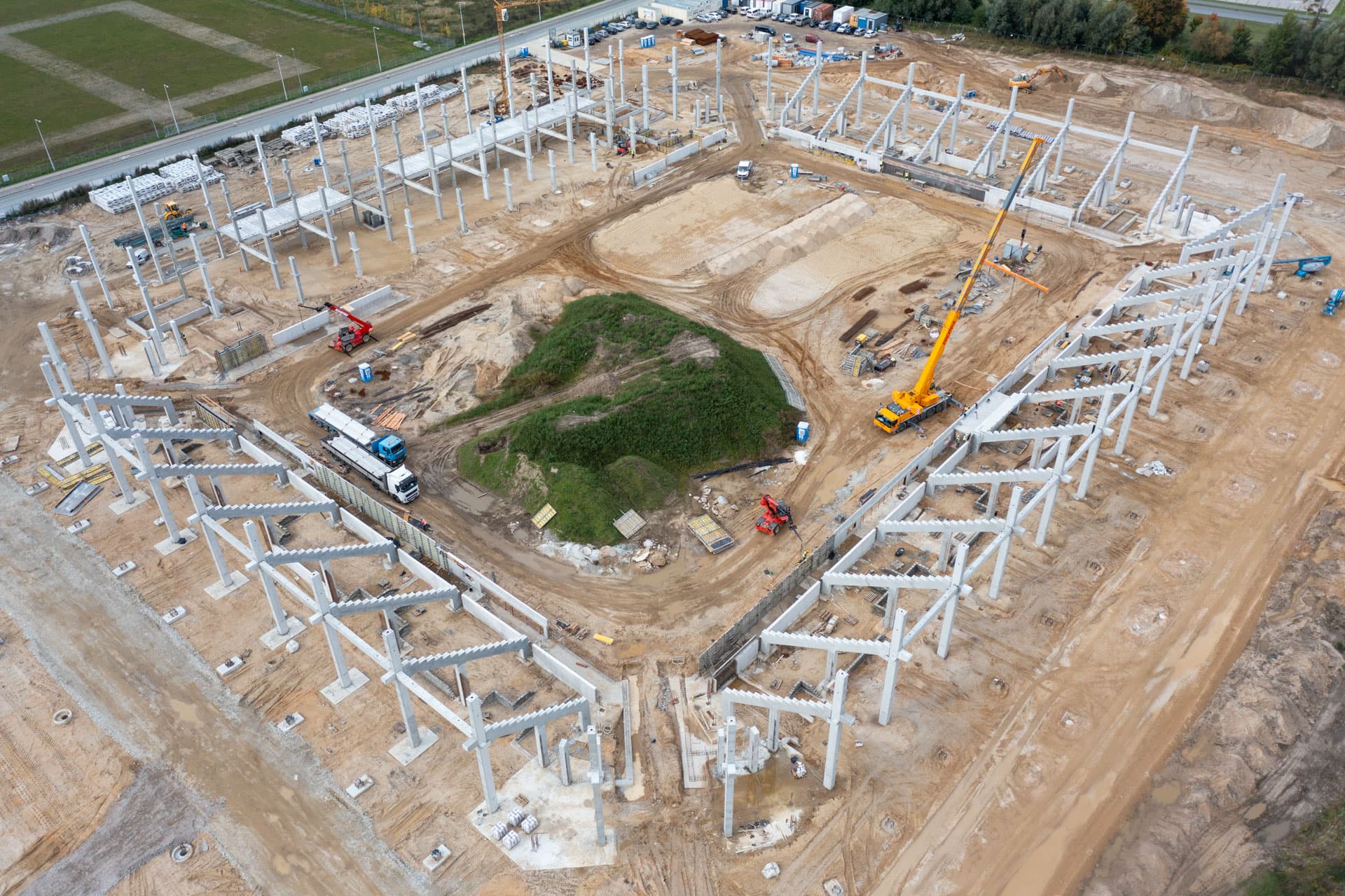
Korzyści z zastosowania prefabrykacji
Zaletą zastosowania technologii prefabrykowanej jest skrócenie czasu realizacji inwestycji, usprawnienie montażu oraz możliwość uzyskania lepszej jakości wykonania niż w przypadku prowadzenia prac na placu budowy. W przypadku Stadionu Miejskiego w Opolu prefabrykaty produkowane są w oddziale firmy Betard w Przyworach, znajdującym się w niewielkiej odległości od miejsca budowy, co ułatwia transport oraz dowóz elementów wielkogabarytowych. Łącznie planowana jest wysyłka ok. 250 samochodów ciężarowych z elementami prefabrykowanymi.
Prefabrykowana konstrukcja stadionu
Obecnie firma Betard produkuje ponad 130 słupów, 200 belek, 570 trybun oraz 270 stopnic. W kolejnym etapie wykonane zostaną biegi schodowe, ściany oraz stropy HCU. Największy przekrój słupów wynosi 50 x 100 cm, a najdłuższy słup ma ponad 17 m. Jednymi z nietypowych produkowanych elementów są słupy o skośnych wspornikach odchylonych od osi o 67,5°, umiejscowione w narożach stadionu, oraz słupy o wspornikach z półkami o długości ponad metr (fotografia 4). Na słupach opierają się belki obwodowe, podstropowe oraz belki zębate, stanowiące podparcie trybun, na których montowane będą siedziska oraz stopnice. Zaprojektowano dwa rodzaje trybun, o przekroju litery L, stanowiące najniższy i najwyższy rząd, oraz trybuny zębate znajdujące się na pośrednich rzędach. Elementy wykonano ze spadkami poprzecznymi, których zadaniem jest poprawne odwodnienie.
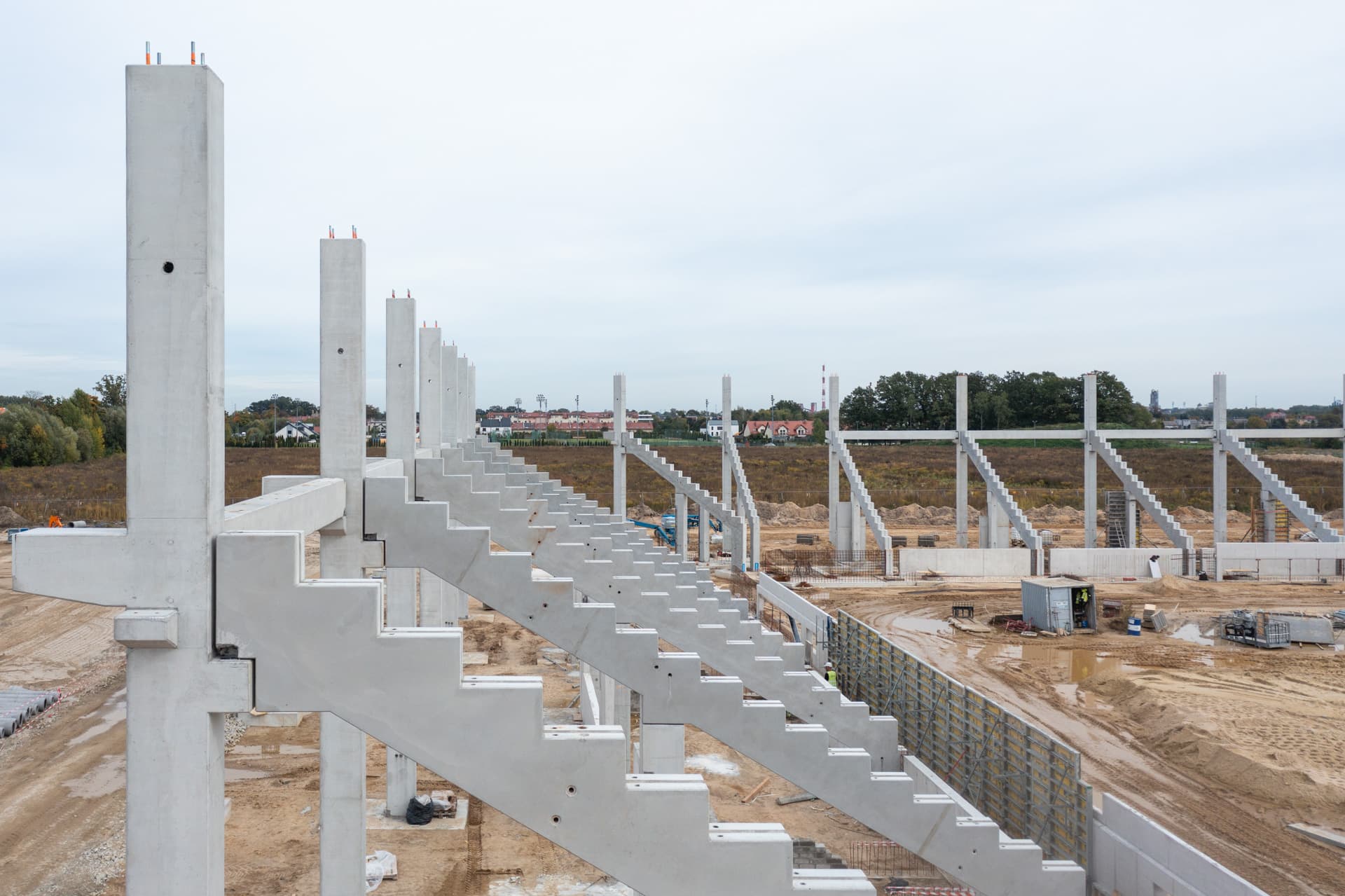
Materiały wykorzystane w produkcji
Do produkcji elementów wykorzystano stal B500SP, beton klasy C35/45 i C45/55 oraz cement portlandzki wieloskładnikowy żużlowo-wapienny CEM II/A-M (S-LL) 52,5N. Charakteryzuje się on szybkim przyrostem wytrzymałości w czasie, krótkim czasem wiązania, dobrą urabialnością oraz dużą wytrzymałością na ściskanie. Należy do cementów ekologicznych ze względu na zastąpienie w jego składzie części klinkieru dodatkiem żużla i wapienia, dzięki czemu zmniejsza się ślad węglowy. W celu poprawy ścieralności betonu oraz jego odporności na warunki atmosferyczne, do produkcji mieszanek betonowych zastosowano kruszywo granitowe. Ze względu na zaprojektowanie mieszanek o konsystencji ASCC/SCC wykorzystano zmielony kamień wapienny jako stabilizator oraz wysokostężone superplastyfikatory, których zadaniem jest znaczna redukcja wody w mieszance. Wpłynęło to na zmniejszenie stosunku wodno-cementowego, co jest kluczowe w przypadku bardzo rygorystycznych wymagań dotyczących trwałości betonu. Uwzględniając wymaganą w projekcie klasę ekspozycji dotyczącą mrozoodporności, użyto również domieszki napowietrzającej, aby uzyskać normowy parametr napowietrzenia – powyżej 4%. Dodatkowo w okresie podwyższonej temperatury zastosowano domieszkę opóźniającą wiązanie na bazie sacharozy w celu zmniejszenia ciepła hydratacji oraz zminimalizowania potencjalnego skurczu w elementach wielkogabarytowych (o dużym przekroju poprzecznym).
Montaż elementów
Montaż elementów na budowie rozpoczął się na początku sierpnia br. Najpierw zamontowano prefabrykowane słupy, które są pierwszym pierścieniem stadionu, co pozwoliło na wykonanie prac monolitycznych. Obecnie montowane są belki i trybuny (fotografia 5). Zakończenie prac montażowych planowane jest na pierwszy trymestr 2023 r., a następnie prowadzone będą prace wykończeniowe. Koniec budowy ma nastąpić w grudniu 2024 r.
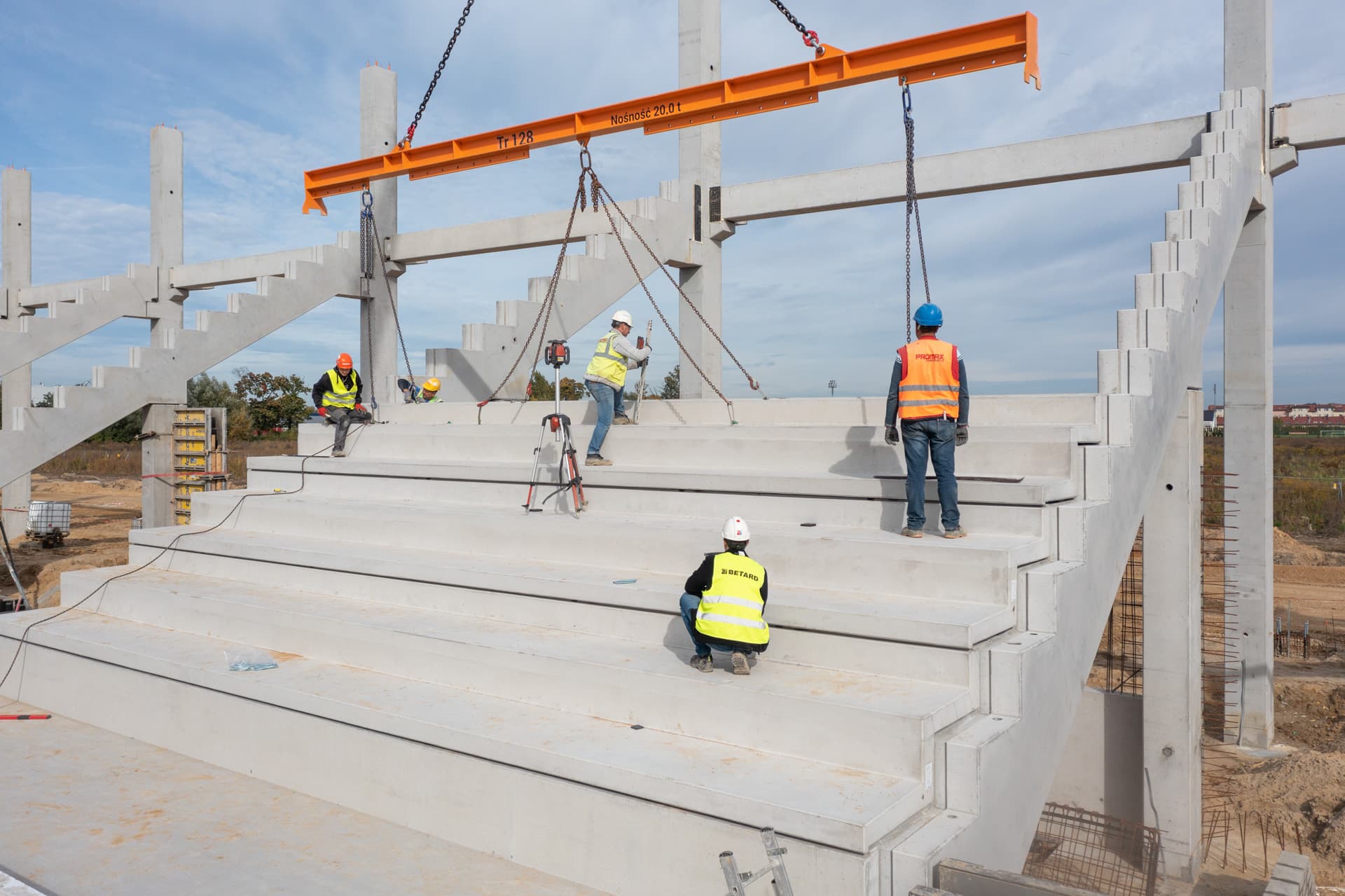
Fot. 5. Montaż prefabrykowanych trybun